
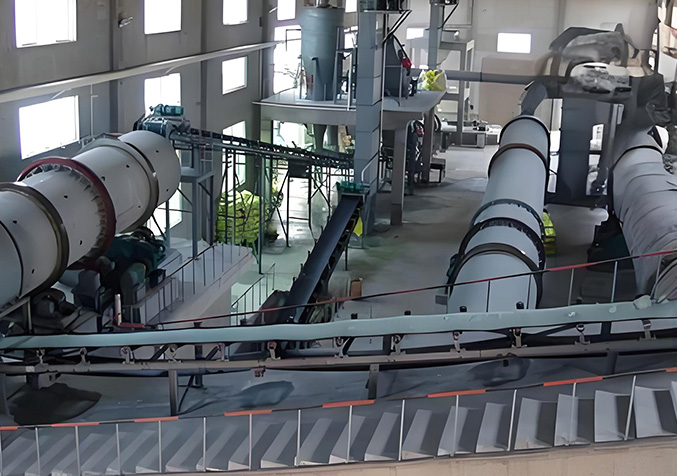
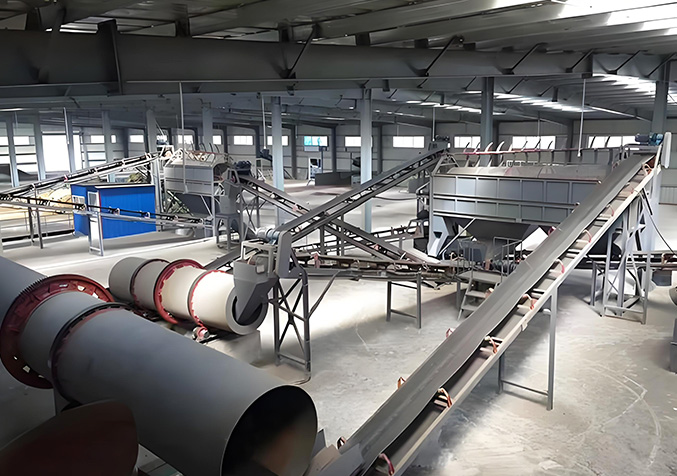
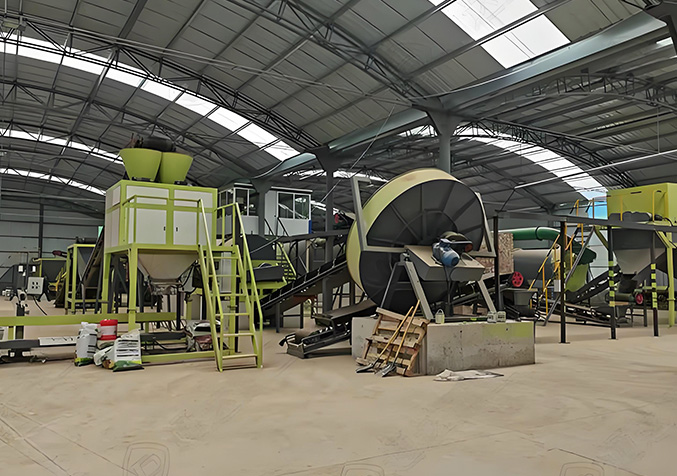
Organic Compound Fertilizer Production Line
Capacity: 0.5-30 t/h
Heat Source:Suitable for biomass, natural gas, diesel, coal, etc.
Application: Widely used for drying chicken manure, cattle manure, pig manure, poultry manure, and other agricultural wastes, biogas residue, kitchen garbage, etc.
Product Introduction
The rapid development of intensive farms has led to the accumulation of livestock and poultry manure, agricultural waste, food waste, and kitchen waste, which pose a serious environmental pollution problem. However, these materials are valuable resources that can be used for the production of feed and fertilizers. Therefore, their development and utilization are essential for promoting animal husbandry and crop production, reducing food waste, and increasing agricultural productivity and income.
To address this issue, Jiuhe has developed a comprehensive set of equipment that facilitates the production of organic fertilizer. This equipment is capable of efficiently fermenting, drying, granulating, and mixing animal waste and various agricultural, food, kitchen, and other waste residues. The production line encompasses the entire process, from raw material collection to finished product packaging, resulting in a complete solution for organic fertilizer production.
Introduction of Cow Manure, Pig Manure, Chicken Manure
1.Cow manure is a slow-acting fertilizer that contains 14.5% organic matter, with N ranging from 0.30% to 0.45%, P ranging from 0.15% to 0.25%, and K ranging from 0.10% to 0.15%. While it has the lowest organic matter content among livestock manure, it is still considered a highly beneficial soil fertilizer.
2.Pig manure, with its fine texture and complex composition, contains 15% organic matter but relatively lower nutrient content. It has N ranging from 0.5% to 0.45%, P ranging from 0.6% to 0.5%, and K ranging from 0.35% to 0.45%. Its high nitrogen content and carbon to nitrogen ratio of 14:1 make it easily decomposable by microorganisms.
3.Chicken manure is a nutrient-rich fertilizer that can be used to make green organic fertilizer or chicken feed. It contains 89.8% dry matter, 28.8% crude protein, 12.7% crude fiber, 14.4% digestible protein, 28.8% nitrogen-free extract, 2.6% phosphorus, 8.7% calcium, and essential amino acids such as histidine, methionine, leucine, lysine, and phenylalanine. Proper processing and utilization of chicken manure can result in higher efficiency compared to other manure types, with each ton of sticky chicken manure containing 11.35 kg of N, 10.44 kg of P (as P2O5), and 5.45 kg of K (as K2O). Additionally, chicken manure is an excellent feedstock for biogas production due to its high organic matter content.
Working Principle
Complete organic fertilizer production line:
1.The first step in the production line is the fermentation process of organic matter. During the preparation stage, the compost is transported to the mixer for thorough mixing and turning to accelerate the fermentation rate.
2.The next process involves crushing the compost blocks using a crusher to prepare it for the pelleting process. If the compost fermentation is satisfactory without any lumps, this step may be skipped.
3.For recipes requiring multiple materials and to improve processing efficiency and accuracy in proportioning the ingredients, an automatic batching system with a number of quantitative belt scales can be utilized. However, if the production is pure organic fertilizer, this step can be omitted.
4.The main step of the production line is the pelleting process, which utilizes a disc pellet machine (rotary pellet mill) for fertilizer granulation. Our equipment can automatically produce pellets of various shapes that meet customer requirements. After fertilization, the pellets can slow the release of fertility, reducing the frequency of artificial fertilization.
5.To reshape the pellet shape and enable better storage, the fertilizer's humidity should not exceed 14%, requiring the use of a drum rotary dryer for drying fertilizer pellets.
6.After drying, the fertilizer pellets must be cooled to increase their hardness, which can be achieved using a roller cooling machine.
7.The screening process is crucial, where a trommel screen is used to select pellets of moderate size, while small and large pellets are re-crushed and re-ground.
8.Coating the fertilizer granules is necessary to prevent particle adhesion. This is accomplished using a roller coating machine.
9.The final process in the production line is the packing process, where an automatic packing machine is used to pack the fertilizer pellets into bags for sale.
10.A dust removal system is employed to collect the dust generated from all processes.
11.Supporting facilities such as belt conveyors and bucket elevators are essential in connecting the different steps of the production line.
Product Parameters
Model |
Chicken manure(m³/hour) |
Cow manure(m³/hour) |
Total power (kw) |
Energy consumption(Standard coal)(kg) |
TDOF12 |
1-2 |
2-3 |
22-30 |
150 |
TDOF24 |
2-4 |
3-5 |
26-40 |
150 |
TDOF36 |
3-6 |
5-7 |
35-50 |
140 |
TDOF68 |
6-8 |
8-10 |
40-60 |
140 |
TDOF1220 |
12-20 |
15-25 |
65-80 |
125 |
TDOF2530 |
25-30 |
30-40 |
90-120 |
125 |